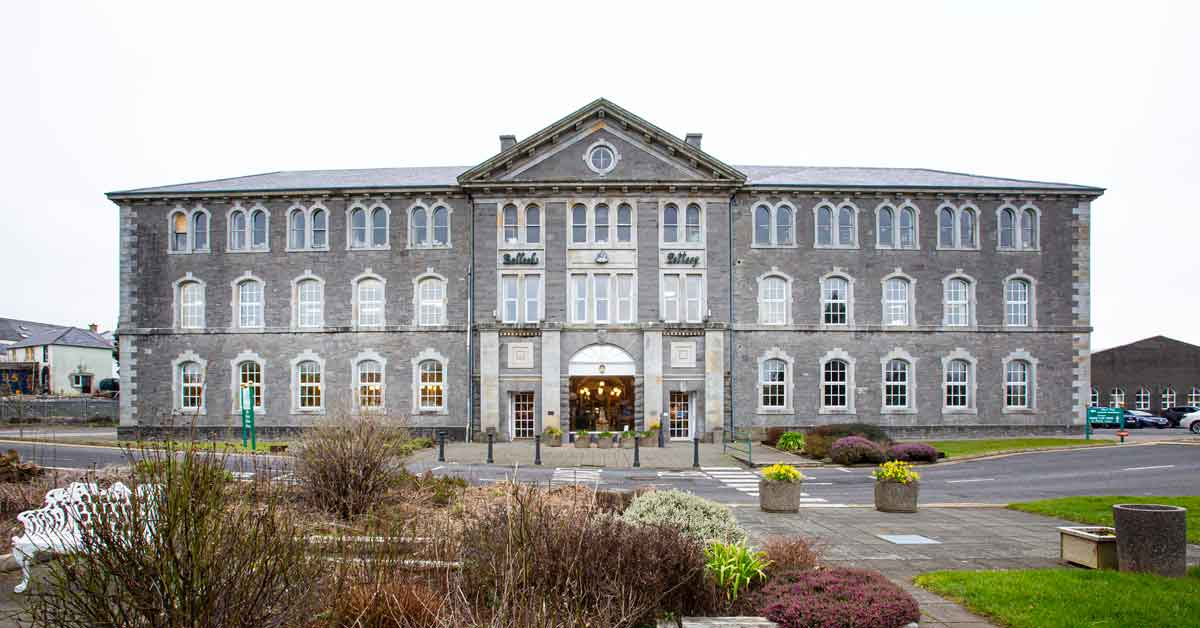
Belleek Pottery was established in 1857 and holds a special place in Ireland's cultural and commercial heritage. Located in the quaint village of Belleek in Co Fermanagh on the banks of the River Erne, it is home to Ireland's oldest working fine china pottery. The skill and craftsmanship has been passed down through the generations keeping the art alive over the last 160 years. Each piece of pottery passes through a special process that touches 16 pairs of hands to get to the final product. The factory produces more that 100,000 pieces of pottery a year.
Factory Tour
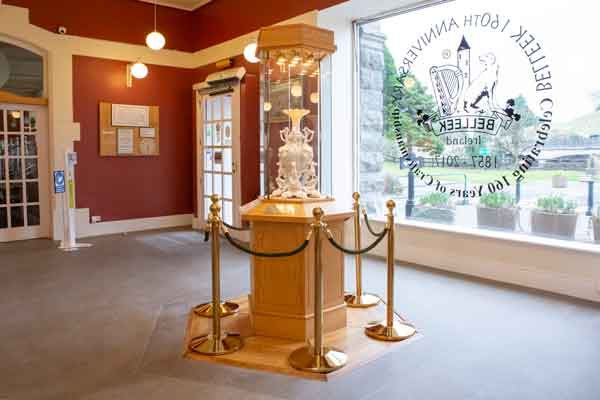
The Creative Irish Gifts team had the pleasure of touring the Belleek factory. On arriving at Belleek Pottery, we were instantly struck by the immense nature and heritage which exists inside the building itself, including a bell which has been hanging from the main reception area for the past 100 years.
We were then invited to speak with master artisans, touch and feel the porcelain and meet with a few of the artisans. We were amazed to see their craft in action! Follow along below to see how they go from an idea to a finished product.
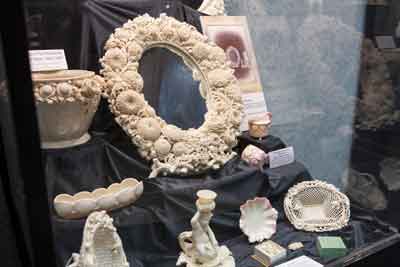
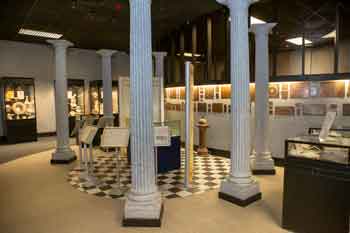
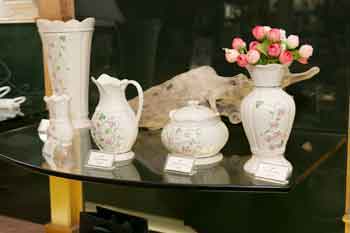
The Design Process
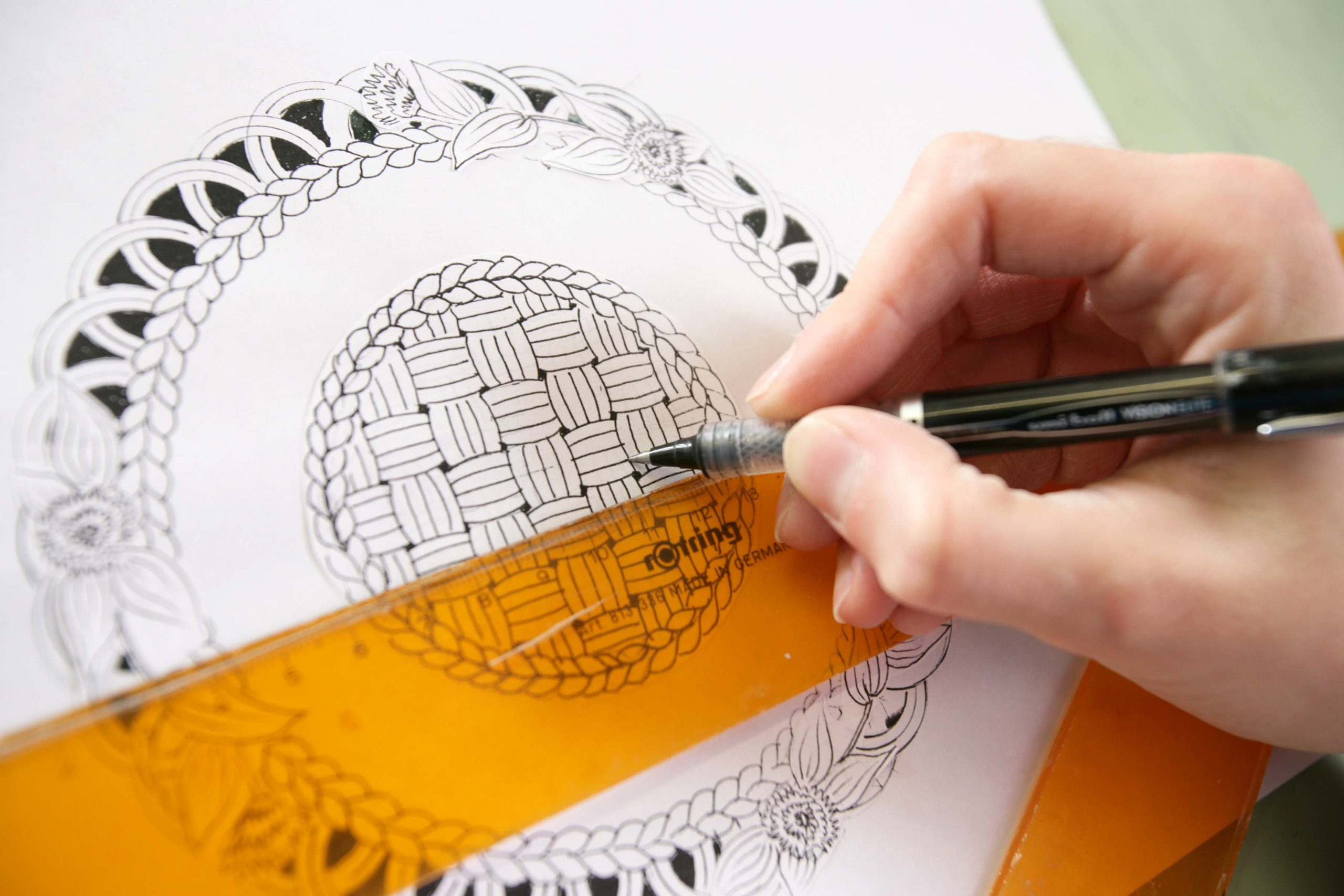
During our tour, we were lucky enough to visit the Belleek studio and see how these models are created. Claire, head designer at Belleek, walked us through the process of designing and creating the pieces before showing us some of the historical molds that have been used over the years. She also gave us a peek into one of her favorite parts of her job: testing out new designs on Belleek artists to make sure they meet high standards!
3D Modeling
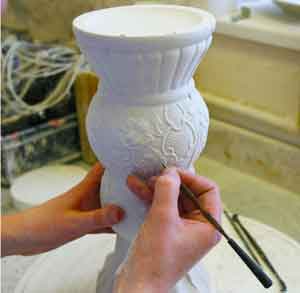
The 3D plaster or clay master models are a faithful replication of the drawing, showing all intricate details and reliefs on the surfaces. Carving these models into a new pattern, it may take 2 days to finish small pieces like an ornament, while larger pieces may require weeks and sometimes months to complete.
Making Molds
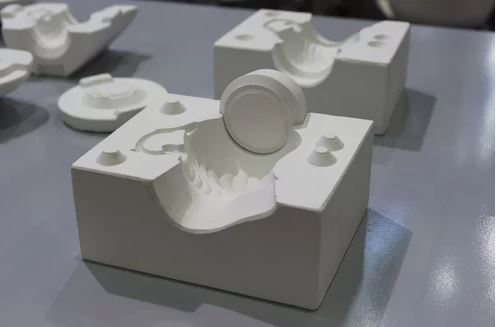
Slip Casting
Slip is the material poured into the working molds that eventually becomes Belleek Parian China. It is a creamy colored liqud formed by a mixture of clay, feldspar and frit. The slip is made fresh each day at Belleek.
Belleek artisans pour slip into the working mold and let it sit until it forms a layer on the inside of the mold. This layer is called the Cast.
Excess slip is then poured off to allow the cast to dry. As it dries, it shrinks away from the mold and can then be gently removed. The slip has now become clay, which is refered to as the Green Ware stage of the procees and where the artist begin the fettling stage.
Artist cleaning and prepping mold for use
Slip being poured into a mold and left to cure
Fettling & Kiln
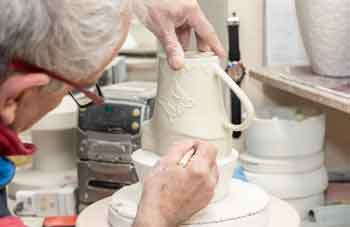
Kilns are slowly fired up to 1,200 degrees centigrade to solidify the casts. Firing up and cooling down has to be done slowly because a sudden change in temperature can cause the piece to shatter. One fired, the ware is refered to as the biscuit. One of the more risky phases of the pottery process is the firing step. Shrinkage on the product can be as large as 15% from the Green Ware dimensions. Each pieces goes throug rigourous inspection after the firing phase. Any piece that does not meet Belleek's high standards is detroyed.
Video of Belleek artist fettling greenware before going to the kiln
Basket Weaving
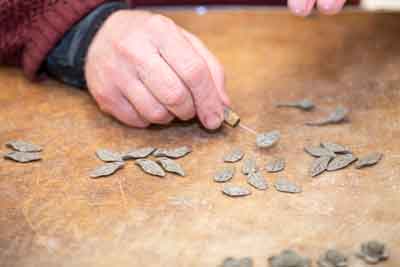
The art of basket-making began in Belleek Pottery in 1867, by William Henshall. He trained the local apprentices in the art and passed on the tradition and craft of basket and flower making, thus beginning a long-standing tradition that continues today.
In the years since then, this craft has been expanded to include more intricate designs but the heart and process remains the same.
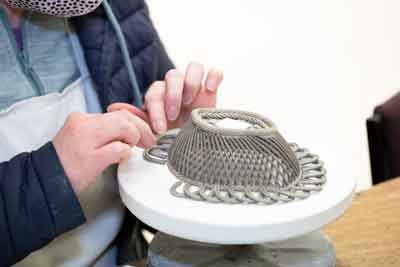
The production of such intricate and meticulous detail requires the use of a more pliable substance than that used on other Belleek products. The clay is then pressed into spaghetti like strands. The base of the basket is hand woven using a weave of two, three or four strands. The body, feet, flowers, stems, buds, twigs and shamrocks are all made entirely by hand. Should a flower require sixty petals, each part of the flower is crafted one piece at a time until the whole intricate blossom is completed. After the artist finishes the design, the piece heads to the kiln and then to paint.
Glazing & Hand Painting
Once the products are removed from the kiln they are each hand dipped in Belleek's signature white glazie formula one at a time. Then each peice goes back to the kiln for a process called gloss firing. This binds the gloss to the Parian at 1,000 degrees. When the peice is set it can then it can be hand painted.
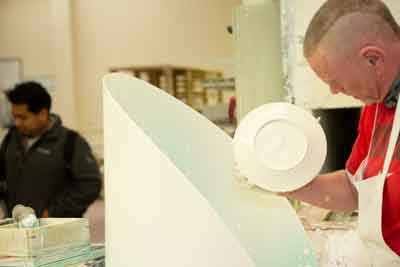
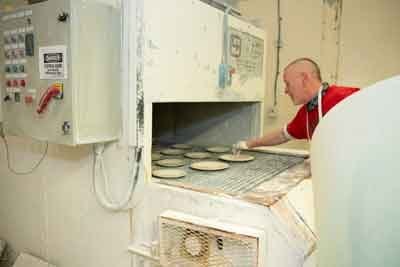
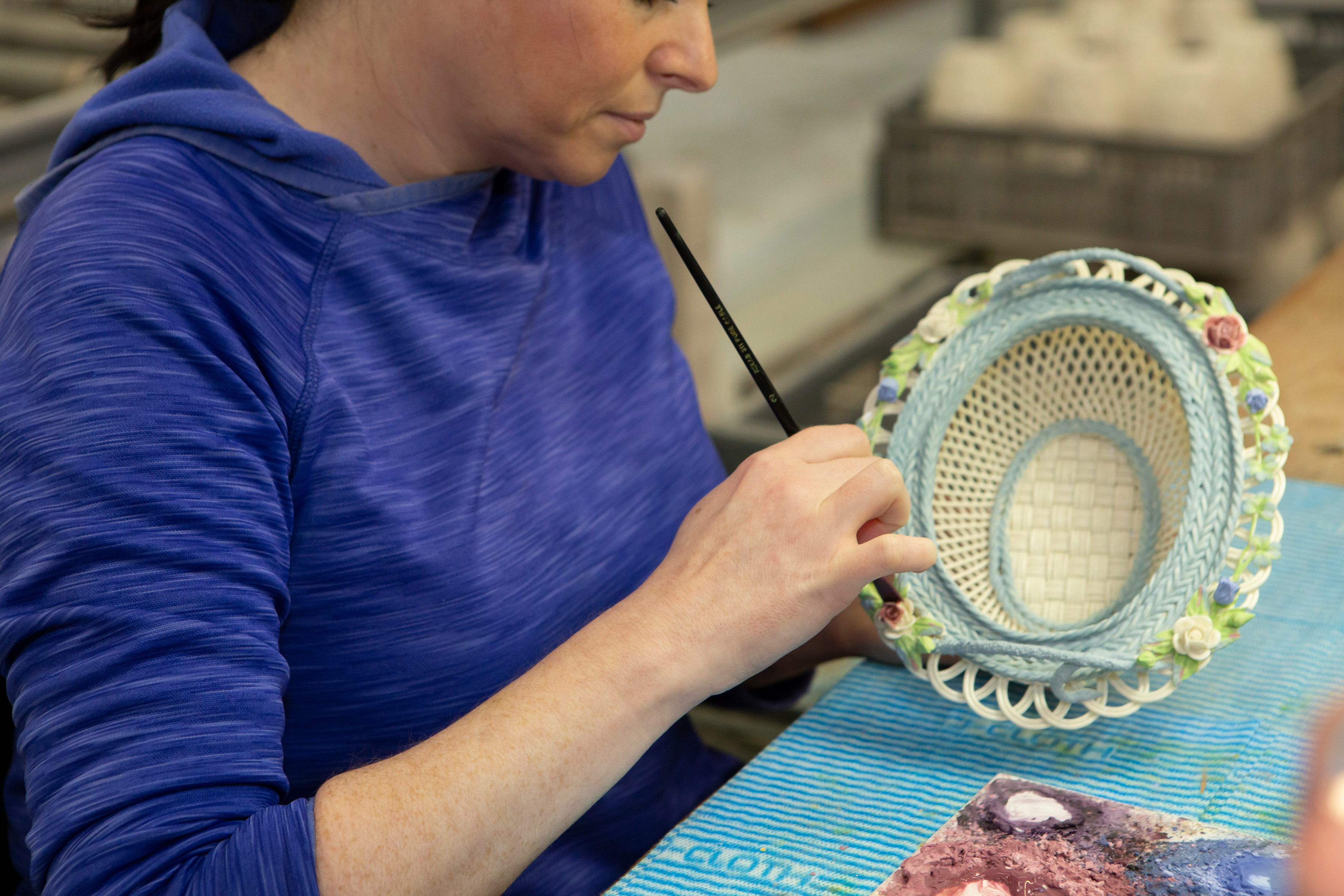
Watch a Belleek hand painting in action below